When you are running a business that relies heavily on logistics, there’s always the threat of failure. Your decisions get affected by threats – whether it’s the threat of an overly competitive market, financial threat, or the threat of employees making mistakes. Business analysts have divided these threats into various types of risks- two of which are strategic and operational risks.
Strategic risks result from decisions about your services or products. So, what is operational risk? Technically, operational risks are everywhere. They exist in the way you carry out decisions. For instance, even if your products and services are right for your market, weaknesses in your supply chain may make it challenging to generate the profits.
A supplier refusing to do business, a warehouse burning down, labor disputes slowing down or stopping work, or roads getting washed away in flood are just some operational risk examples.
Described by the Basel Committee on Banking Supervision, operational risk is defined as “the risk of loss resulting from inadequate or failed internal processes, people and systems, or external events. As such, operational risks capture business continuity plans, environmental risk, crisis management, process systems, and operations risk, people-related risks and health and safety, and information technology risks.”
According to the Basel Accords, operational risk can include internal fraud, external fraud, damages to business assets, business disruption and system failures, employment practices and workplace safety, delivery and process management, and client products and business practices.
It might be tempting to play the odds when it comes to operational risks. “What are the chances that a fire will destroy my warehouse or that drivers will go on strike just ahead of the Holiday season?” you might think. Unfortunately, many logistics-intensive businesses take that bet and often lose.
Operational risks have the potential to impact the reputation and financial stability of your business significantly. This is the main reason risk managers have started to adopt best practices in operational risk management (ORM)- to protect their businesses from this low-likelihood, but high-cost events.
What is Operational Risk Management?
Incompetent processes, ineffective hardware, and failure of systems can cripple your business operations. Communication breakdowns, employee errors, and frauds, and cybercrime also present potential risks. The key to risk mitigation is to look carefully at those elements, then establish a contingency plan to prevent breakdowns that lead to costly reputational and financial damages.
Businesses must have robust processes in place for reducing operational risks, as these processes can have a significant impact on their ability to thrive and make profits. A lack of strategies for mitigating operational risks may result in functional failures, leading to a crisis in day-to-day management.
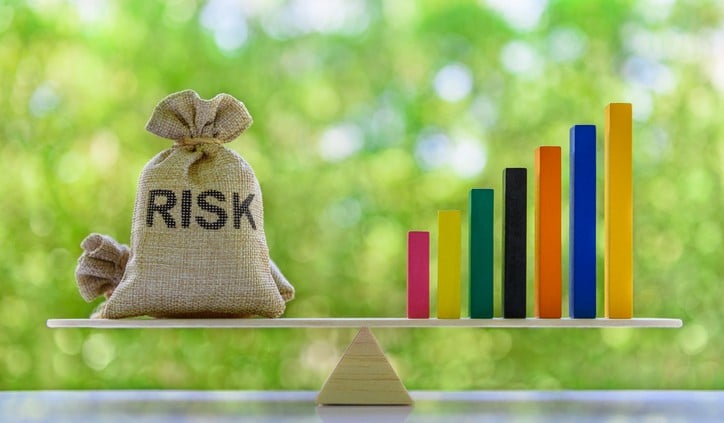
An essential aspect of a business’s approach to risk management is its risk appetite statement, which acts as a bridge between strategy and operations, and leads to effective business decisions. However, operational risk appetite should not only be an integral part of the overall risk framework, but it should also be measurable. According to experts, poor operational risk management in logistics may lead to a financial crisis, and eventually, the collapse of business operations.
Want To See For Yourself How Route4Me Can Boost Your Profits?
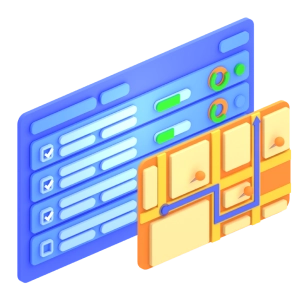
How To Mitigate Operational Risks?
Operational risks can interfere with a business’s ability to function and are usually out of your control. However, that doesn’t mean you shouldn’t take steps to prepare for the unexpected and reduce operational risks. For instance, sprinkler systems and smoke detectors have proved useful in saving warehouses from fire, while security cameras can eliminate employee thefts. More complex risks require strategic planning, such as monitoring the financial stability of vendors and building a diverse supplier base.
One of the ways to manage operational risks is by purchasing interruption insurance. Though the coverage varies, these policies reimburse the business to a large extent for losses due to unexpected events like floods, fires, and power outages.
Another way to mitigate operational risks is by developing strategies that align with risk evolution. The process begins with a risk assessment of factors that may impact business objectives.
Here are some practical ways to manage operational risks in the future:
You need to ensure adequate controls at every stage of risk evolution. The earlier you establish controls, the easier it will be to identify and mitigate risks. Most businesses do an operational risk analysis using the following ten-step approach.
Step One: Segregating tasks
Segregation of duties reduces the chances of internal risks and theft by preventing an employee from taking advantage of the numerous aspects of processes or transactions.
Step Two: Limiting complexities in existing processes
Decreasing complexities in business processes will radically mitigate operational risks. You can achieve this by eliminating manual activities and limiting the number of people involved during a critical business process.
Step Three: Reinforcing ethics
Ethics can be reinforced by combining the values of individuals with business principles.
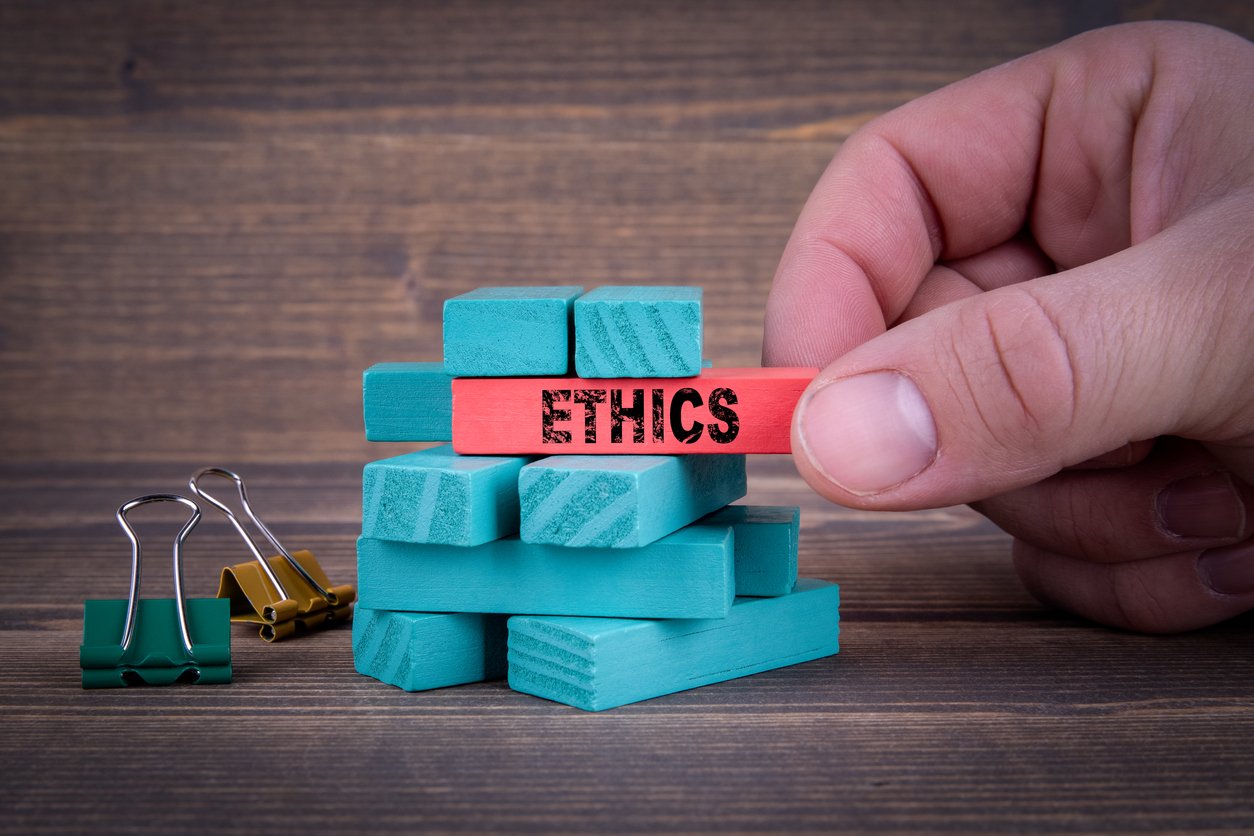
Step Four: Finding the right people
Having people with the right skillset can reduce issues related to process execution. This will also help you improve workforce utilization, enhance quality, adhere to timelines, and create fewer process breakdowns.
Step Five: Monitoring regularly
Your processes will be more effective when you have well-designed key performance indicators (KPI) in place. KPIs are critical for identifying and mitigating risks, provided they are monitored and reviewed regularly.
Step Six: Periodic operational risk assessment
Regular assessments of every facet of the operational risks will make day-to-day management smoother. It is essential to be risk-ready by gauging IT assets, workforce skill sets, competencies, business strategies, and processes.
Step Seven: Learning from experiences
Risk incidents and remedial activities implemented in the past will help you design effective strategies to handle future risks. Previous risk occurrences will support real-time amendments and help you create both a stronger and more proactive risk management framework.
Step Eight: Ensuring Asset Safety
Despite using the best technology and advanced tools, your equipment can still break down, which may cripple your business operations. You can reduce the risk of equipment failure by adhering to regular preventive maintenance. Have processes in place to ensure that small issues are identified and resolved quickly so they don’t turn into bigger problems down the road that could result in financial losses.
Step Nine: Getting Insurance Coverage
Despite all the precautions you can take, if something does happen, you need to have adequate insurance cover to compensate for damages and losses. Having an insurance policy that covers negative impacts on your business could mean the difference between a small or large disruption in your operations.
Step Ten: Understanding Regulations
Whatever business you run, make sure all of your practices are adhering to the law of the land, including details like employee wages, health and safety standards, taxes, and licensing and certification influence your day-to-day operations. Do not let ignorance get you in trouble.
What Are The Advantages Of Operational Risk Management?
With so much on the line, every business that relies heavily on logistics should develop an operational risk management process that guides their operations and prevents financial and reputational risks.
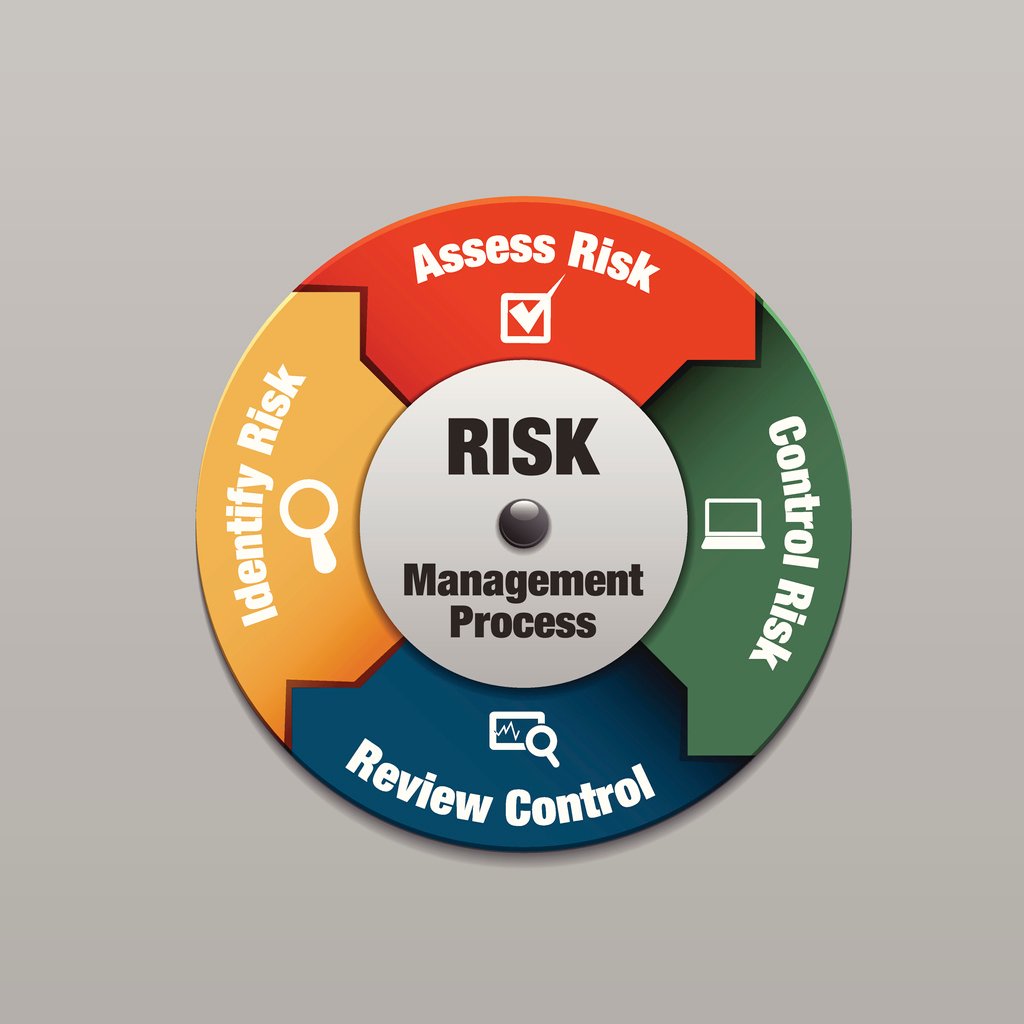
A business’s ability to manage risk will serve as a powerful tool to attract clients and investors who believe their business and reputation are in good hands.
When a business fails to implement an effective operational risk strategy, they communicate to their clients and employees that risk management is not its focus. This may have a detrimental effect on employee morale and winning new clients.
Most logistics companies have a risk management process, as their concern is keeping the supply chain running smoothly. In fact, even clients ask carriers about their risk management policies that can reduce potential shipment risks these days. Without a strong strategy, your clients will go elsewhere because they have too much at stake to take chances.
Everyone has a role to play in operational risk management. Employees should be given clear guidelines that explain their responsibilities when it comes to safeguarding the organization’s finances and reputation. Operational risks are always lurking in the background; successful businesses ensure effective management and prepare for the worst while hoping that it never happens.
Want To See For Yourself How Route4Me Can Boost Your Profits?
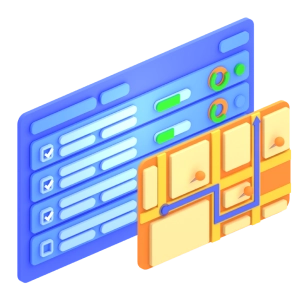